Датой основания компании можно считать 2014 год. Тогда будущему основателю компании Дмитрию Шейкину пожаловался коллега на работе — “двери болтаются”. Это причиняло коллеге много неудобств. Разобрав дверь, он понял, что проблема в двух износившихся пластиковых деталях – фиксаторах ограничителей дверей.
Коллега пытался решить проблему самостоятельно. Он вырезал фиксаторы по образу и подобию старых из полиэтилена. Но они стёрлись уже через месяц. Следующей попыткой было изготовление фиксаторов из фторопласта. Их постигла та же участь.
В то время Дмитрий занимался печатью на 3D принтере. И предложил своему коллеге распечатать фиксаторы. Выбор материала пал на нейлон, поскольку другие пластики для 3D печати хрупкие и могли быстро стереться. Нейлоновые фиксаторы «проходили» 1 год.
Почитав форумы, Дмитрий понял, что проблема фиксации дверей есть у многих автовладельцев. Тогда и пришла идея производства фиксаторов на разные автомобили.
ПОЧЕМУ ОТКАЗАЛИСЬ ОТ 3D-ПЕЧАТИ
Число заказов росло, и стало ясно — нужно расширяться, но 3D-принтер не подходит для серийного производства. Печать и обработка отнимали много времени, а качество фиксаторов оставляло желать лучшего. Дмитрий начал подбирать другие варианты изготовления фиксаторов. Путем проб и ошибок пришел к методу литья в силиконовые формы. Лучшим материалом оказался американский полиуретановый пластик.
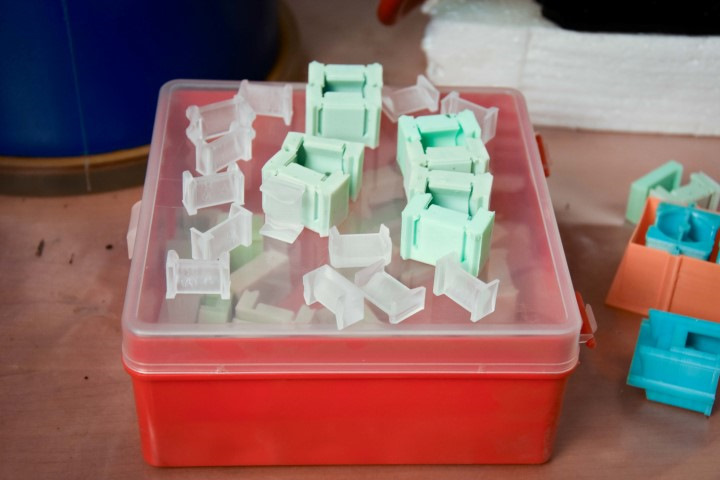
Для испытания фиксаторов из полиуретанового пластика Дмитрий сделал ручной испытательный стенд. Вместе с женой мы вручную по очереди моделировали 15000 циклов открывания и закрывания двери (это примерно 3 года эксплуатации). Когда я вскрыл ограничитель, фиксаторы были изношены наполовину. Материал показал себя не плохо, но поиски оптимального материала продолжились.
КАК ФОРМИРОВАЛСЯ АССОРТИМЕНТ
Чтобы сформировать ассортимент, нужно было заказывать и разбирать каждый тип ограничителей и дорабатывать стертые фиксаторы. Так создавался первый ассортимент фиксаторов на разные модели автомобилей. А чтобы клиентам было удобнее делать заказы, мы создали и запустил сайт plastik-avto.ru/
ПОЧЕМУ ПРОДОЛЖИЛИ ПОИСК НОВОГО МАТЕРИАЛА
Но не всё шло гладко. Обнаружилось, что некоторые фиксаторы не выдерживали реальных условий эксплуатации. Пришлось анализировать возможные причины поломок. Из-за перепадов температур качество поставляемого жидкого пластика в разных партиях было разным. Один раз пришла поставка перемороженного пластика, но Дмитрий узнал об этом уже от недовольных покупателей. Фиксаторы ломались, скрипели и не фиксировали дверь.
Поиск подходящего материала и эксперименты продолжились. Дмитрий добавлял в пластик графит, углеволокно, пробовал полиуретановые резины. Но ничего из этого не работало должным образом. В конце концов был выбран прозрачный американский литьевой пластик, который по износостойкости показал себя лучше всего. Прочность достигалась выдерживанием в печи в течение 6 часов. Правда, был и у него один минус: двери начинали скрипеть на морозе.
Литье в формы отнимало много времени. Спрос превышал возможности производства. Выход один — пора менять и материал, и всю технологию производства. Это означало начать всё заново. Выбросить всю коллекцию силиконовых форм, на которые ушло столько времени и денег. Вложить еще больше в новое оборудование и материал.
В сентябре 2016 года Дмитрий покупает станок с ЧПУ и партию качественного износостойкого пластика.
С тех пор фиксаторы стали производиться из графитокапролона. Этот пластик служит долго, поэтому на все ремкомплекты действует гарантия – 3 года.
Чтобы автоматизировать производство, закупалось всё больше дополнительного оборудования для обработки деталей. Дома становилось тесно. В июне 2017 года домашнее производство переместилось в офис, были наняты первые сотрудники.
КАК СЕЙЧАС ПРОИЗВОДЯТСЯ РЕМКОМПЛЕКТЫ ОГРАНИЧИТЕЛЕЙ ДВЕРЕЙ
Сейчас ремкомплекты производятся методом литья на термопластавтомате. На литье Plastic Auto перешли в 2019 году. Это позволяет делать детали аналогичными оригиналам и повысить производительность. Поэтому все ремкомплекты из ассортимента всегда в наличии. Материал изготовления – полиамид 6, наполненный графитом, дисульфидом молибдена и фторопластом. Этот состав лучше всех показал себя на испытаниях.
В 2020-2021 году Plastic Auto взял курс на расширение ассортимента и разработку шестерней для разных узлов автомобиля. С тех пор разнообразие ремкомплектов значительно выросло:
Привода люка
Рулевой рейки
Привода сиденья
Привода антенны
Трапеции дворников
Привода боковых зеркал
Привода трапеции дворников
Привода дроссельной заслонки
Натяжитель пружины дворников
Штоков актуатора люка бензобака
Втулок-шарниров трапеции стеклоочистителя
Полный ассортимент на сайте ➡ plastik-avto.ru/
Так одна маленькая деталь — фиксатор, дала начало целому производству качественных ремкомплектов для разных узлов автомобиля. Деталей, которые помогают экономить десятки тысяч рублей автовладельцам по всему миру.